Roll Formers
Quality Makes Us Global
Roll Forming at Global Forming
An incredible variety of metal parts and components can be manufactured from flat sheet metal, mostly steel, with the roll forming process and automation. Depending on the final shape and profile needed, multiple sets of consecutive rollers each bend the metal strip in some incremental way toward the final result. A variety of other metalworking operations can be incorporated at various points along the roll forming production line.
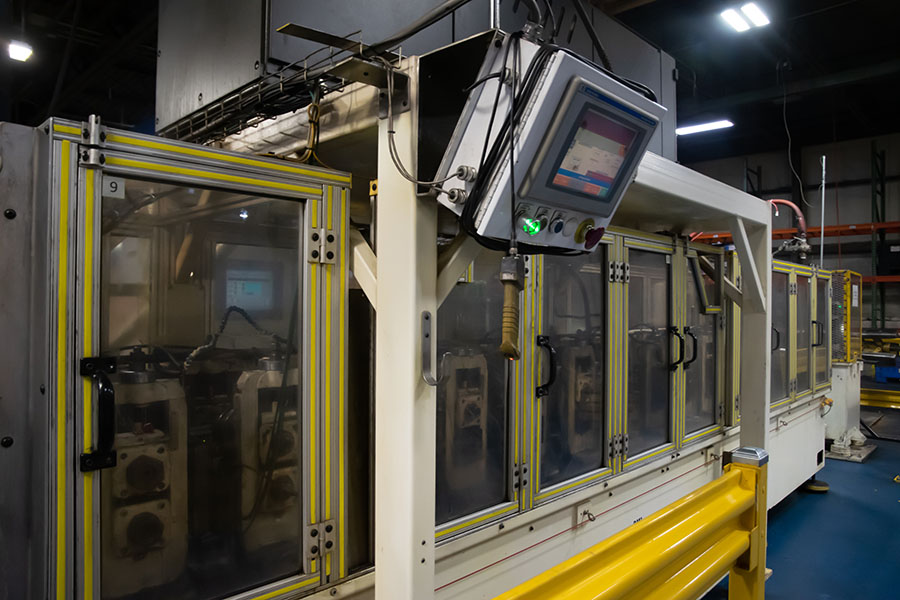

Flexibility in State-of-the Art Roll Forming Capabilities
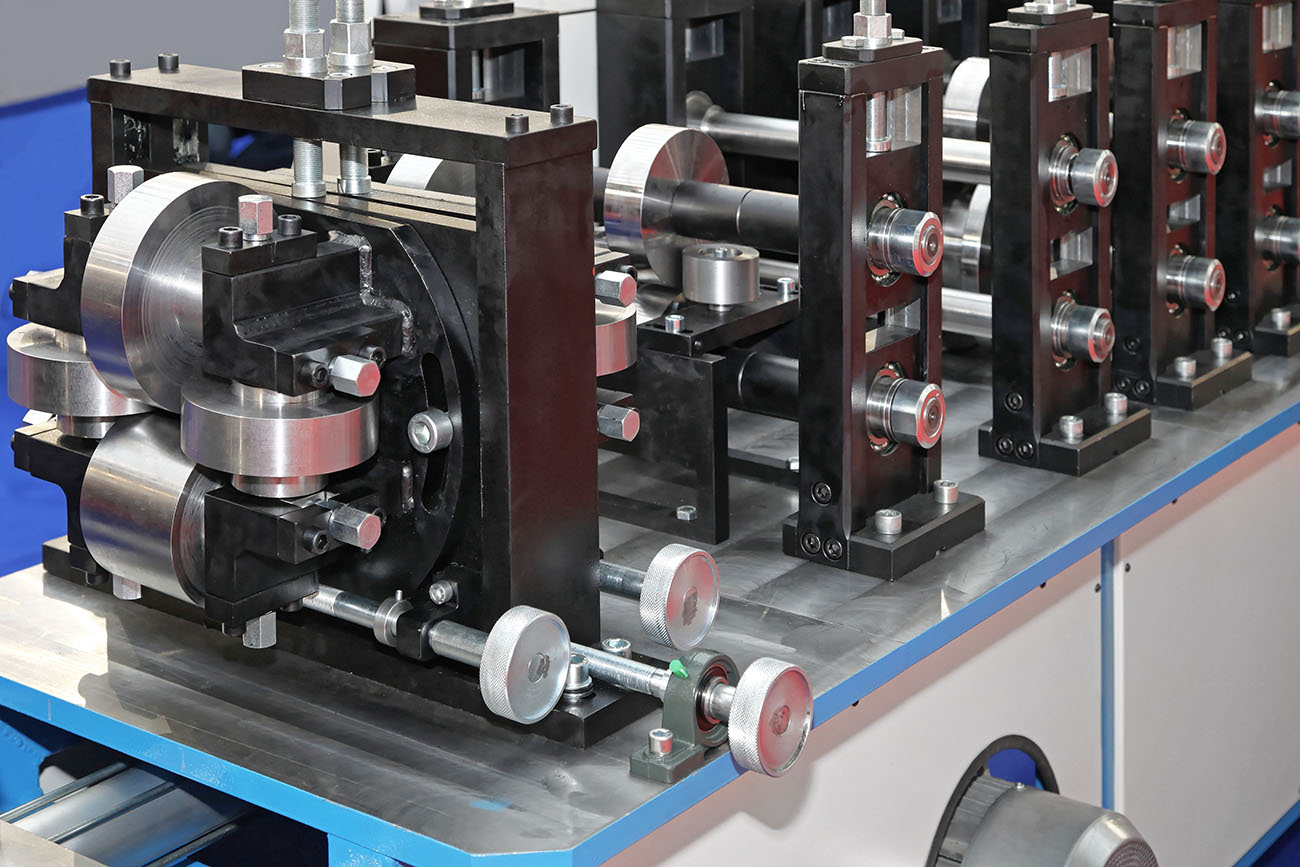
Common sheet metal thicknesses or gauges that can be handled by roll forming machines range from 0.004–1.25 inches (0.1015 to 31.75mm) thick. The sheet metal typically arrives at the roll forming mill in large coils. One end of the coil is fed through an entry guide on the roll forming line to ensure optimal alignment of the material as it approaches the first set of rolls. The entire process takes place at room temperature (cold-forming), so it’s not as energy-intensive as hot-forming processes.
There are many benefits to roll forming as a metalworking manufacturing process relative to other techniques, as described below:
Extrusion as a manufacturing process is great for softer metals such as aluminum, tin, copper, magnesium, zinc, and softer low carbon steels. High carbon steel, titanium, and harder alloys are less amenable to extrusion, which is why roll forming is often a better choice to achieve the desired profile. Extrusion is also limited in how thin the final profile can be. Roll forming works well on a wider range of metals (especially harder metals) and thinner profiles, which can save money on material costs. Extruded profiles in aluminum often need to go through an aging process to ensure stability, which adds a significant amount of time to the production process. Roll formed metal profiles do not require any aging.
Relative to other metal manufacturing processes, roll forming often represents more streamlined production and lower overall costs while achieving precision processing to very tight tolerances with superior part uniformity and better surface finishes.
While this means a significant up-front investment in tooling costs for any given profile, once the roll dies are tooled, they experience very little wear during use and will facilitate high-volume production runs for years at a time, even if the length of the final part needs to be changed, which is easy to accomplish through adjusting the cut off function.
At Global Forming, we’ll take your designs for roller dies and have the expert tooling staff we work with review them to ensure manufacturability before tooling begins. We’ll manage the entire tooling process for you to ensure superior tooling results for your projects roller dies.
Roll forming can be used for building exit devices such as push bars on doors (also called crash bars and panic bars). Many of the metal components for HVAC parts and assemblies can be produced by roll forming, such as the metal frame that holds a filter material in place. Given the flexibility and versatility of roll forming, there are many more industries that make use of roll formed metal parts and components, including aerospace, appliances, construction, energy, solar, tube and pipe, and many more.
We look forward to hearing from you through the contact us page of our website, by phone at 317.290.1000, or by email to rfox@globalforming.us to discuss whether our roll forming services are the right fit for your project.