Stretch Bending Metal Forming Process
Quality Makes Us Global
Stretch Bending Metal Shaping at Global Forming
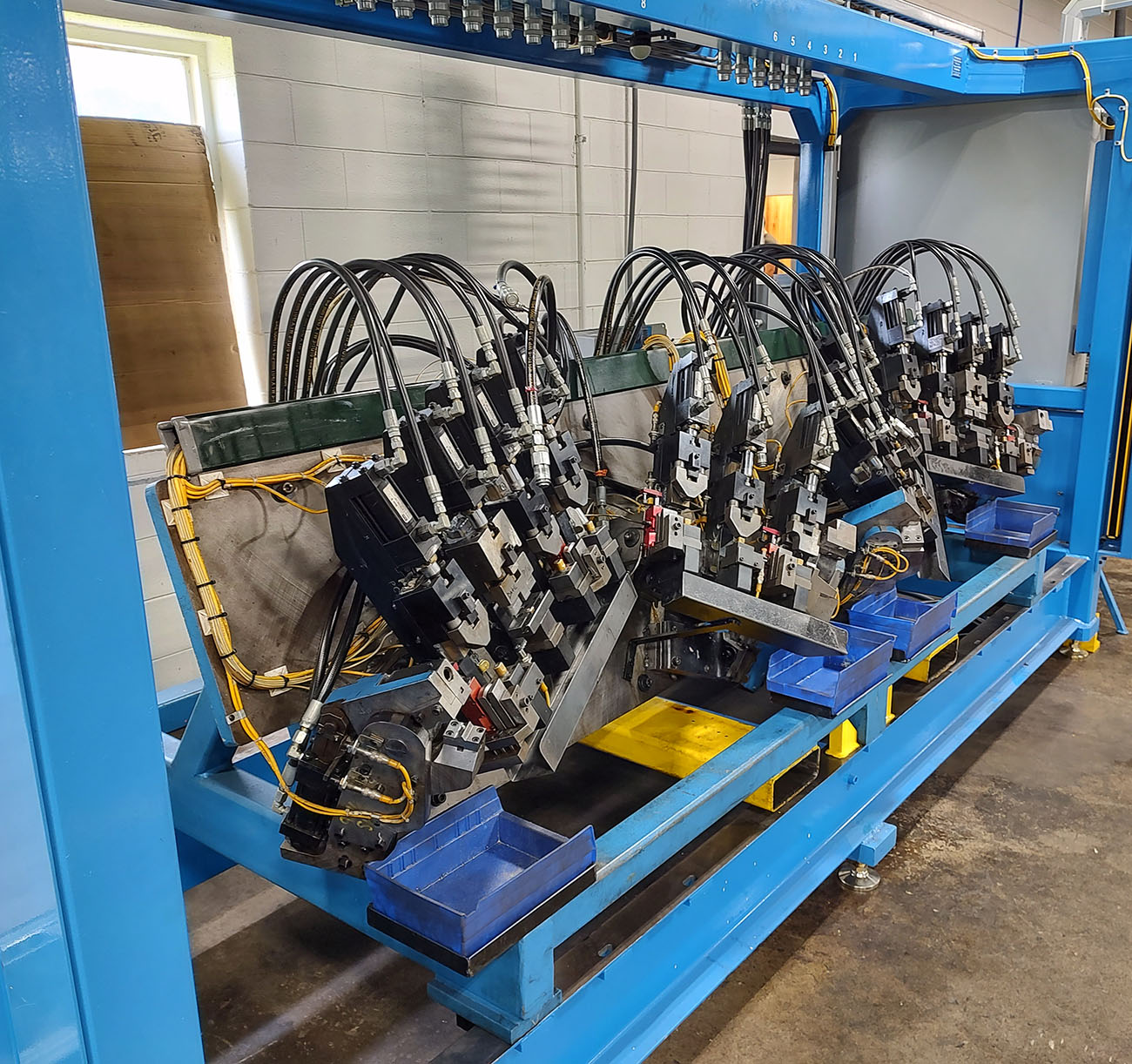
The Rise of Stretch-Bending for Better Results
The workpiece is pressed onto or around a machined form (a die, also called a form block) to achieve a part with one or several different curve radii. In the industry, the machine accomplishing the work may be called a stretch bending machine, stretch press, a stretch former, and so on. The stretching is what compensates for the compression forces on the inner surface of the workpiece and basically pulls out any wrinkles or buckles before they can happen.
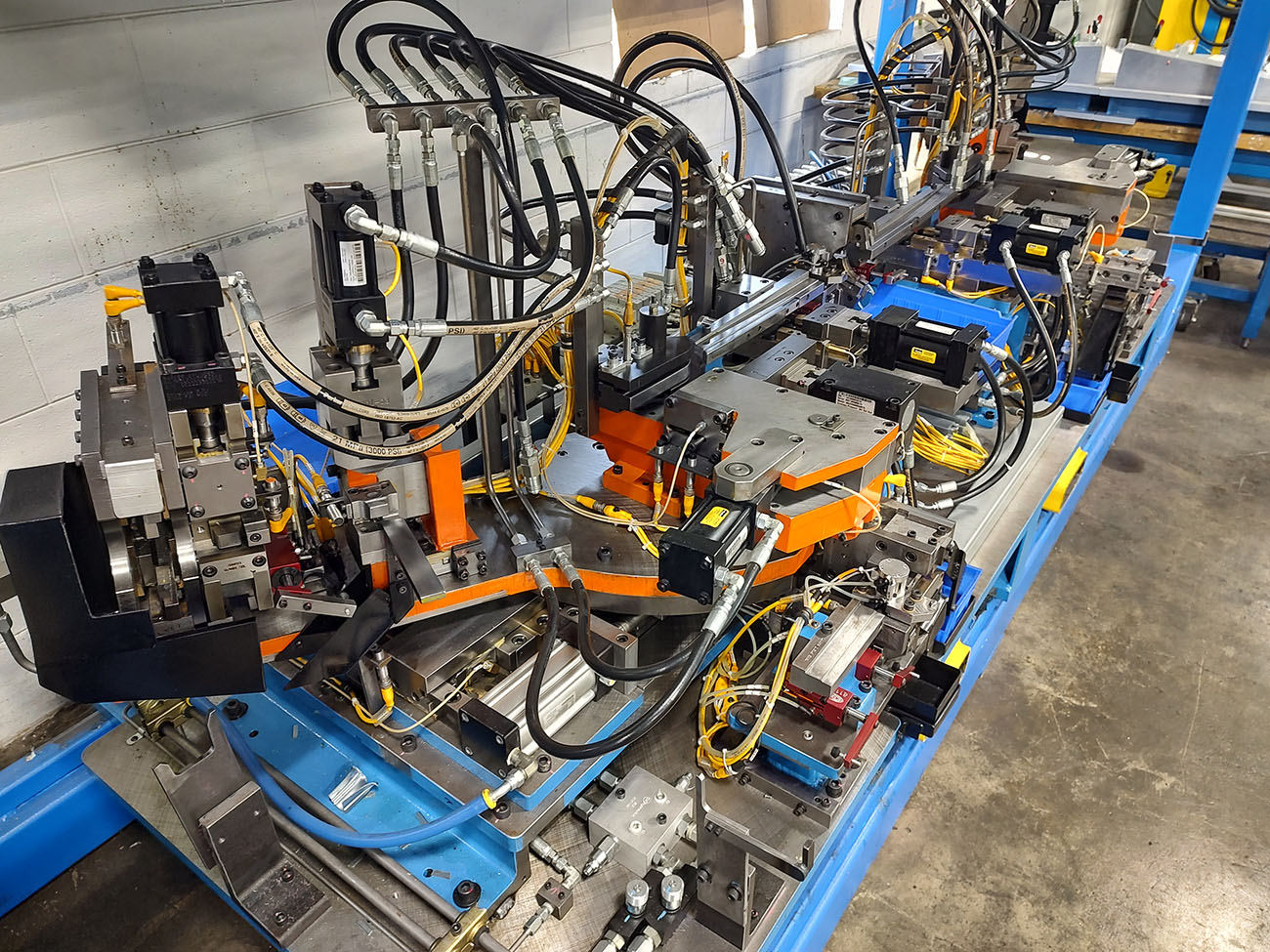
Reduced Material Costs
Energy Efficiency
Unparalleled Accuracy
Flexibility
Quality Parts
Stronger Parts
Reduced Spring-back
Low Residual Stresses
Lower Tooling Costs
Process Efficiency
Cost Effective
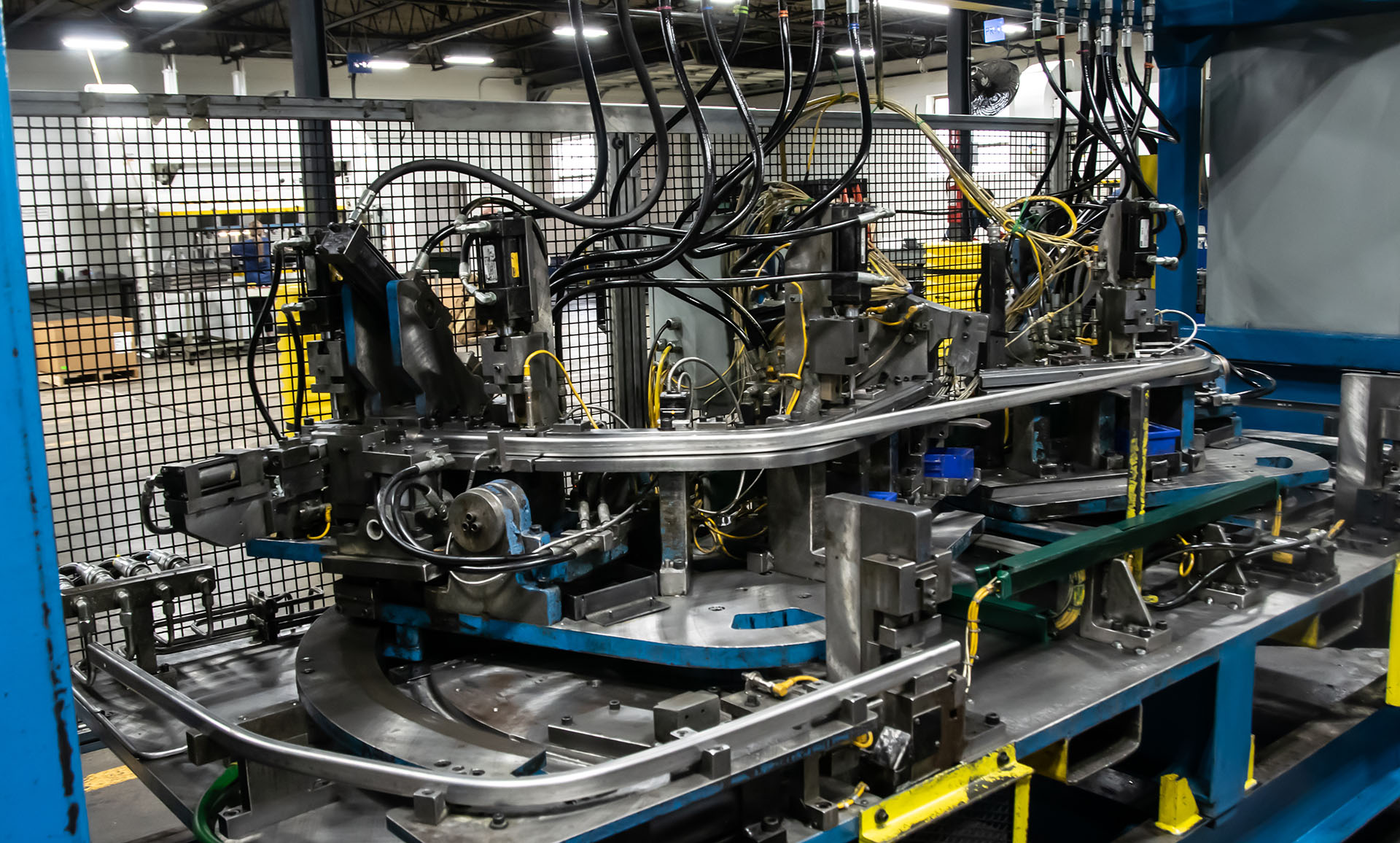
Is stretch bending or stretch forming the right metal shaping technique for your project? It depends on a lot of different factors. Feel free to contact us and our team of experts will help you determine if Global Forming’s stretch bending capabilities are the right fit for your project.